Porosity in Welding: Identifying Common Issues and Implementing Best Practices for Avoidance
Porosity in welding is a prevalent problem that frequently goes undetected until it causes significant troubles with the stability of welds. In this conversation, we will certainly explore the vital aspects adding to porosity development, examine its destructive effects on weld performance, and go over the ideal methods that can be adopted to minimize porosity event in welding procedures.
Typical Reasons of Porosity
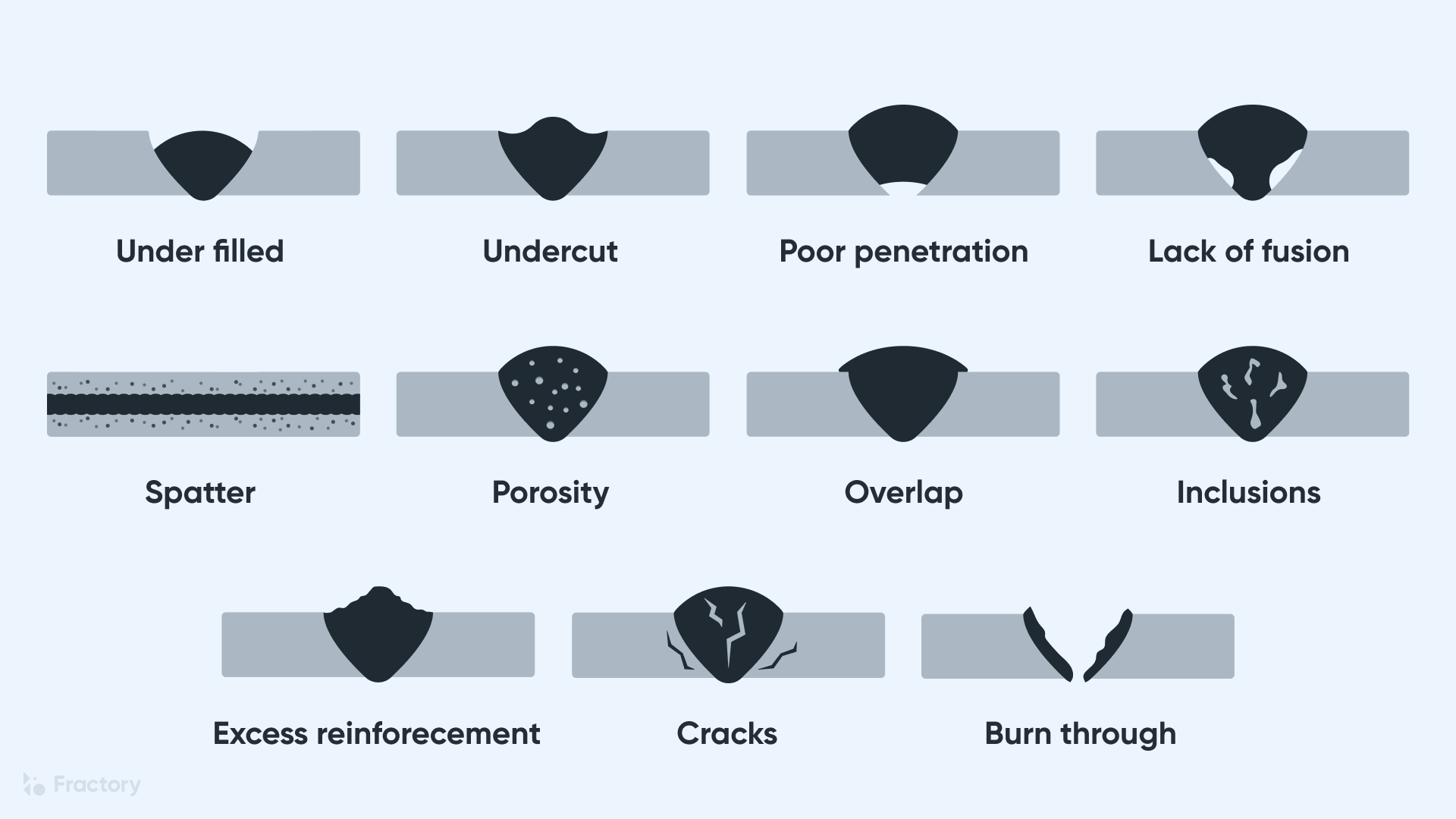
Utilizing unclean or wet filler products can introduce contaminations right into the weld, contributing to porosity concerns. To minimize these common reasons of porosity, comprehensive cleansing of base metals, proper shielding gas selection, and adherence to optimal welding specifications are necessary practices in achieving high-grade, porosity-free welds.
Influence of Porosity on Weld Top Quality

The visibility of porosity in welding can considerably compromise the architectural honesty and mechanical residential properties of bonded joints. Porosity produces gaps within the weld metal, compromising its general strength and load-bearing capacity. These gaps act as stress focus factors, making the weld extra at risk to splitting and failure under applied lots. Furthermore, porosity can minimize the weld's resistance to corrosion and other ecological elements, further reducing its durability and efficiency.
One of the key consequences of porosity is a decline in the weld's ductility and durability. Welds with high porosity degrees tend to display reduced impact strength and decreased capacity to deform plastically before fracturing. This can be especially worrying in applications where the bonded parts are subjected to vibrant or cyclic loading problems. Porosity can restrain the weld's ability to effectively transfer pressures, leading to premature weld failure and potential security hazards in important structures. What is Porosity.
Best Practices for Porosity Avoidance
To boost the structural honesty and high quality of welded joints, what specific measures can be executed to decrease the incident of porosity during the welding process? Utilizing the proper welding strategy for the particular material being bonded, such as adjusting the welding angle and gun setting, can better protect against porosity. Regular assessment of welds and instant remediation of any type of problems determined throughout the welding procedure are necessary methods to protect against porosity and generate high-grade welds.
Value of Correct Welding Methods
Implementing correct welding methods is extremely important in making certain the structural integrity and quality of bonded joints, building on the foundation of effective porosity prevention steps. Welding techniques straight impact the general stamina and resilience of the bonded framework. One crucial element of appropriate welding strategies is maintaining the proper warmth input. Too much warmth can cause boosted porosity because of the entrapment of gases in the weld swimming pool. Conversely, inadequate warm might lead to insufficient fusion, producing possible powerlessness in the joint. Furthermore, making use of the suitable welding criteria, such as voltage, current, and travel speed, is important for accomplishing sound welds with minimal porosity.
Additionally, the selection of welding procedure, whether it be MIG, TIG, or stick welding, ought to straighten with the specific requirements of the job to guarantee optimal results. Correct cleaning and prep work of the base steel, as well as choosing the appropriate filler product, are also important elements of basics skilled welding strategies. By adhering to these ideal techniques, welders can reduce the danger of porosity formation and generate high-quality, structurally sound welds.

Examining and Top Quality Control Procedures
Quality assurance steps play have a peek at this site a crucial duty in confirming the honesty and integrity of bonded joints. Evaluating procedures are necessary to find and stop porosity in welding, guaranteeing the strength and longevity of the end product. Non-destructive screening methods such as ultrasonic screening, radiographic testing, and aesthetic assessment are generally employed to determine prospective problems like porosity. These techniques permit the analysis of weld high quality without endangering the stability of the joint. What is Porosity.
Carrying out pre-weld and post-weld assessments is also crucial in keeping high quality control standards. Pre-weld evaluations include verifying the materials, tools setups, and tidiness of the workspace to avoid contamination. Post-weld examinations, on the other hand, examine the last weld for any flaws, including porosity, and confirm that it meets defined requirements. Executing a comprehensive high quality control strategy that consists of detailed screening treatments and assessments is extremely important to minimizing porosity concerns and making sure the overall top quality of welded joints.
Conclusion
Finally, porosity in welding can be an usual issue that affects the high quality of welds. By determining the typical root causes of porosity and carrying out finest try here methods for prevention, such as proper welding techniques and testing procedures, welders can guarantee high quality and dependable welds. It is essential to prioritize avoidance approaches to minimize the event of porosity and preserve the honesty of welded frameworks.